25 Days to Market: The Inside Story of How Xerox Pivoted to Manufacture Much-Needed Hand Sanitizer
As the first bottles of hand sanitizer rolled off a Xerox production line in Ontario and Webster, N.Y., last week, more than a dozen employees—wearing protective gear and employing social distancing—were on hand in both locations to celebrate a feat of applied materials expertise and organizational nimbleness.
In just under a month, a group of 50 employees across the company worked together to quickly bring to market hospital-grade sanitizer in response to the Covid-19 pandemic. It all started with a Friday email from Xerox CEO John Visentin, and the company’s senior R&D leaders began to brainstorm ideas.
“John challenged all of us in an email to look at what we could do with a few activities around Covid, so we sat down as a little team and came up with a plan,” says Dr. Paul Smith, vice president and director of the Xerox Research Centre of Canada in Mississauga, Ontario. “We’re in R&D and materials formulations is a core strength so, though we’ve never made sanitizer before, it seemed like something we could do at scale.”
That was March 20. Xerox CTO Naresh Shanker weighed in with guidance, suggesting Smith’s team in Canada partner with Yonn Rasmussen, vice president of technology and development, and her colleagues in Webster, N.Y. The groups in Canada and the U.S. quickly joined forces, invoking the famous line from the Tom Hanks movie, Apollo 13, “Failure is not an option.” (Hanks of course had recently been diagnosed with Covid-19.)
Many questions emerged: Where would the company source the increasingly scarce raw materials necessary to make sanitizer? And what containers were needed to deliver it to hospitals?
First came the question of the actual formula. Isopropyl alcohol, a key component, was impossible to source as all kinds of companies raced to produce their own formulations. Hand sanitizer also can be made from ethanol, however, and in late March, public health officials in the U.S. issued new guidelines for hospital-grade hand sanitizer that made using ethanol possible.
Rasmussen’s team discovered an ethanol supplier in western New York. “Literally over a weekend, we started the arduous process of talking to the vendor, figuring out how to transport the ethanol to our facilities, and other logistics,” Rasmussen says. “The company turned out to be in a perfect location, roughly halfway between Webster and Ontario.”
Next, came a series of production questions. Bottling proved to be a puzzle. The group originally planned for 55-gallon drums, but feedback from the field indicated they should produce gallon and half-gallon bottles as well, particularly for the U.S. market. With a focus on safety and speed to market, they came up with a production process with one manufacturing line handling mixing and batching, and another for semiautomatic filling that could be set up in both countries simultaneously.
The final piece concerned sales and distribution. Teams in the U.S. and Canada tackled thorny issues—setting up purchase orders, billing, and other sales logistics—in a torrid, two-week sprint. “We engaged Darren Cassidy’s team to see, what’s the best way to get our product in the hands of hospitals,” Rasmussen says.
The first test batch rolled off the lines in Ontario and Webster on April 16, with deliveries to begin by the end of the month. Production is expected to reach 140,000 fluid gallons in Q2. Demand already outstrips supply and the teams are now looking for ways to increase capacity. Amid the flurry of activity, Smith has reflected on how this project came to be and what we can learn from it. “This experience brings up a lot of thoughts about Xerox for me,” Smith says. “First, we were able as two teams to work in Canada and the United States on a common problem and, in this moment, it was as if a border didn’t separate us—we were able to work as one.”
“And second,” Smith continues, “it’s a reminder of the incredible talent within this company. Whenever Xerox does something, it’s all done correctly, it’s all done the right way. We’ve never made hand sanitizer before, but everything is in place to get it right.”
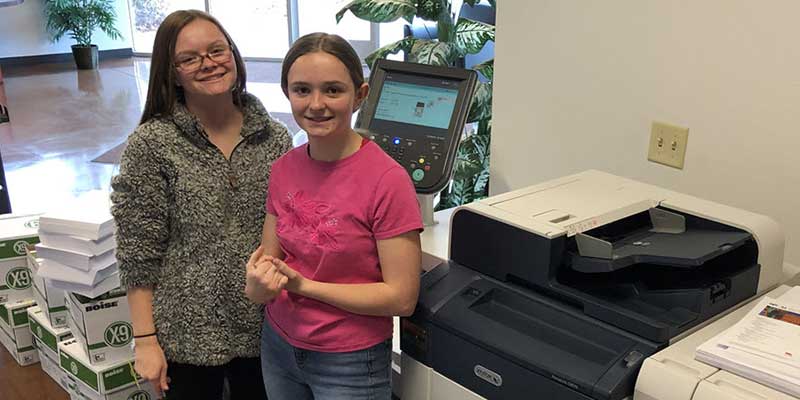
Reno Schools Move Students to Remote Learning Over a Weekend, With an Assist from Xerox
With a surprising number of families that lacked at-home access to computers, the school district reached out to Xerox to help them scale up their printing services as fast as possible.
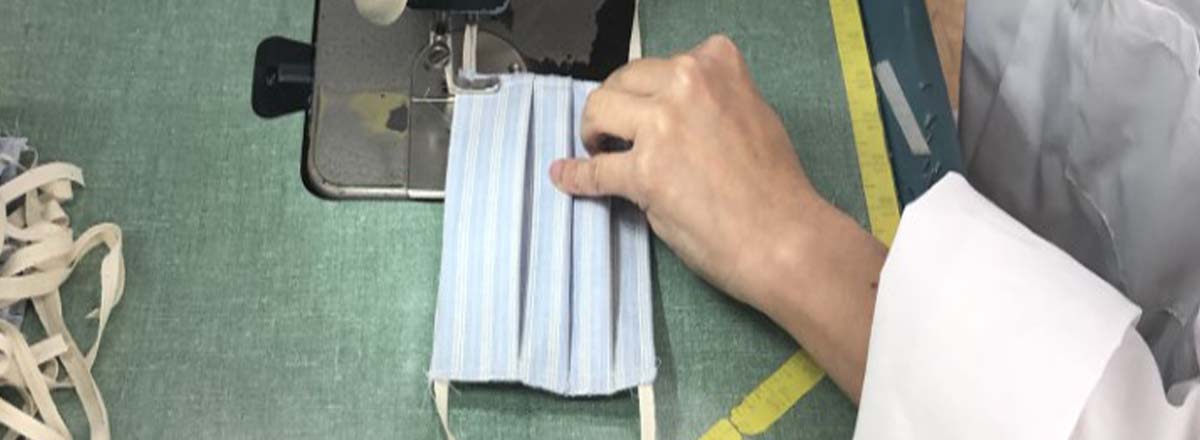
How Xerox Turned Printer Filters into Face Masks
When the call went out at Xerox to think about new ways to use materials on hand to help the coronavirus humanitarian effort, Mark Adiletta, long-time Xerox engineering manager, had a crazy thought: What if we use printer filters to make medical-grade face masks?
Articles connexes
Quocirca désigne Xerox comme leader du développement durable dans le secteur de l’impression
Quocirca, une source majeure de recherche indépendante, de leadership éclairé et d’informations exploitables pour l’industrie de l’impression, a nommé Xerox Leader du développement durable, dans son rapport sur les leaders du développement durable 2024.
Liste des entreprises les plus durables par Corporate Knights
Corporate Knights considère Xerox comme l’une des entreprises les plus durables. Découvrez pourquoi nos objectifs de développement durable et notre feuille de route vers le net zéro place Xerox en tête des autres entreprises de la liste.
Prix – Pacesetter, Keypoint Intelligence, BLI et autres
Les produits et services Xerox ont reçu certaines des distinctions parmi les plus recherchées de l’industrie, notamment Pacesetter, Keypoint Intelligence - Buyers Lab et d'autres Prix dédiés au lieu de travail.
Xerox figure parmi les 100 meilleures entreprises citoyennes
3BL Media a désigné Xerox comme l'une des 100 meilleures entreprises citoyennes de 2022 pour sa transparence et ses performances exceptionnelles en matière d'environnement, de société et de gouvernance (ESG).
Xerox Named One of America’s Most Responsible Companies by Newsweek
Xerox is featured among the top 500 largest public companies in the U.S. for the fourth consecutive year.